Blue Buffalo, now a brand within the General Mills family, first opened the doors of its 450,000 square-foot Richmond, Indiana plant in June 2019. Management knew that for the plant to be competitive, they needed a strong reliability culture and a focus on proactive maintenance and lubrication.
On the culture side, Blue Buffalo had it covered. Plant leadership sat down with the first group of 60 newly-hired “Buffs” and talked about the type of plant and workplace they wanted to create. Together, they developed a very straightforward but powerful policy called the “N.A. Policy.”
“N.A. stands for no a**holes,” said Megan Johnson, Plant Manager. “At Blue, we have very few policies, but we passionately live our values and fiercely protect our N.A. policy. When you keep the problem children out, you don’t have to make an encyclopedia of policies to address them.”
Megan has 11 years of experience at the General Mills brand, and Blue Buffalo Richmond is the third plant she has managed for the organization. She says that the plant was designed with reliability in mind from the beginning, thanks in large part to a previous plant manager who understood the importance of proactive maintenance and lubrication in today’s market.
“I’ve served plants that are 100 years old, and those plants just haven’t grown up with the world-class manufacturing and reliability standards we started out with,” Megan said.
That makes a measurable impact on the bottom line. In today’s uncertain world of supply chain issues and increasing demand for food products, Megan told us, proactive maintenance - especially lubrication - play a major role in the plant’s ability to compete.
“COVID babies or COVID puppies are a totally real phenomenon...we can only meet that demand by proactively maintaining our equipment. Our lube guys and the program we have here truly are a competitive advantage for us.”
Those lube guys are Matt Felix and Kevin Keith. While Matt and Kevin did not start their careers with a focus on lubrication, it’s their bread and butter today. Noria has been a source of knowledge and support for both of them during this process through training and onsite services.
Learning & Preparing
When Blue Buffalo called Noria, they were in the process of designing and building the plant. Before machines were installed, they worked with Noria to ensure that the right inspections, contamination control activities and lubrication procedures would be in place from day one of operations. Over the course of a year, Noria visited the Richmond site six times to identify lubrication points, document procedures and train staff on best practices.
“I learned a lot about the right way to do things from the training with Noria,” Matt said. “Where I came from before Blue Buffalo, it was just: ‘throw some oil in it,’ or ‘throw some grease on it,’ it didn’t necessarily matter what oil or what grease, as long as it had something in it.”
But through Noria’s training courses, Matt has come a long way since those days, having successfully achieved MLT I, MLT II, MLA I, MLA II, and MLA III certifications to supplement what he learned through Noria’s lubrication program development process.
Today, Matt and Kevin are the lubrication experts in their plant. Maintenance technicians come to them for insights and advice on bearing health or related concerns, but it wasn’t always that way.
Early on, Kevin said there was some friction in getting the lubrication program started. Maintenance technicians who had been greasing bearings themselves without the help of a lubrication technician their whole careers were unsure why a skilled position was needed for such a “simple” task: just add grease until you see it purge out the other side, right?

Our lube guys and the program we have here truly are a competitive advantage for us.
Blue Buffalo Lube Guys Matt Felix and Kevin Keith
It wasn’t long before Matt and Kevin had cleared up that common misconception, and things only got better from there as the results of lubrication improvements started to become more obvious.
“Since then, the maintenance guys have learned that we know what we’re doing, and it’s working,” said Kevin. “So now they will say, ‘hey, I noticed that bearing is a little warm - could you take a look at it?’ ”
Roadmap to Success
When Noria helps a plant make improvements to its lubrication program, they follow a three-phase approach of assessment, design and implementation.
Phase one, the AscendTM Assessment, is a three-day process in which a Noria expert walks the plant, capturing details of current lubrication practices and procedures. Then they deliver a complete report, which includes a strategic plan designed to help the plant achieve both quick wins and long-term success along with an overall score.

With the Noria Assessment, we just follow it like a roadmap to lead us to a better place.
Once Blue Buffalo's assessment was complete, it became much clearer where the lube program was going and how Noria would help make it happen.
“With the Noria assessment, we just follow it like a roadmap to lead us to a better place,” Kevin said.
By removing the trial-and-error of building a lube program from scratch, the AscendTM Assessment helps plants quickly determine where they stand and how to pursue their most profitable opportunities first.
“It pays for itself in about a year and a half,” Matt added.
Lubrication Equipment & Machine Modifications
With the assessment complete and the roadmap in hand, it was time to start modifying equipment, installing breathers, sight glasses and other improvements that drive reliability.
“We started looking at all the products we could use to modify our equipment to have a closed system - that was a big focal point in what I wanted to do: have visual sight glasses, quick connects, fill ports, sample ports and desiccant breathers,” Matt said. “Wes and Jeremie would advise me on what products were available or answer questions about installation. They even came out for a week and just helped me work through the installs to get it all done.”
The lube storage room was one of the last pieces of the program to be defined as there was uncertainty on where in the plant it would be located. Matt and Kevin ultimately agreed on a large room that would be divided in two, with one half serving as the lube room. Because proper storage is at the foundation of every successful lube program, the room was equipped with all the necessary components:
- Temperature control system
- Labeling system
- Separation of food-grade and non-food-grade lubricants (and associated hardware)
- Oil Safe systems to prefilter “new” oil
- Storage cabinets
Having these fixtures in place upholds the integrity of a plant’s lubrication program. Without a clean and controlled space, lubricants can degrade significantly before even entering machines. Environmental contamination, temperature fluctuations or cross-contamination can all play a role.
“With it being organized and everything labeled, it definitely makes it faster and easier to find what you need,” Matt said.
“And you’re sure of what you’re doing too,” adds Kevin.
Without clear and easy-to-read labels, lubricant mixing and misapplication run rampant in most plants, leading to unplanned downtime and potentially requiring an entire oil system to be drained, flushed and refilled.
Lubrication Program Management & Optimization
After the program was designed and operations began, Matt and Kevin had to determine how they would manage the program together. The plant is split into two halves of production - pre-kill, where raw ingredients are introduced, and post-kill, where any remaining bacteria in the ingredients has been killed off. To minimize cross-contamination between these two sides, Matt and Kevin familiarized themselves with all lubrication tasks across the plant and switch sides day to day. That way, if one of them leaves or goes on vacation, the other will be able to perform all necessary lubrication tasks with ease.
While their lubrication program is running smoothly, Matt and Kevin are always improving. They log in to their LubePMTM online portal regularly to review AscendTM Assessment data and check in on progress toward larger program goals.
Recently, Blue Buffalo expanded the Richmond plant to meet demand and increase production capabilities, leading to an increase in lubrication points. To maintain efficiency as production increases, the plant is looking into purchasing more automatic lubricators and an FTIR machine to help inform their proactive maintenance strategy.
Winning the John R. Battle Award
Blue Buffalo’s Richmond plant applied for the 2021 John R. Battle Award for lubrication excellence, showcasing their dedication to best practices and continuous improvement. The plant was recognized as the winner of the award at Noria’s Reliable Plant Conference in Louisville, Kentucky in October of 2021.
According to Megan, the award did more than just recognize their contributions to the success of the plant - it also brought more awareness to the company as a whole to the importance of lubrication.
“If you don’t ‘grow up’ around lubrication in your career, you kind of take it for granted. It’s easy to just assume someone is out there doing it - it’s very much an unsung hero of reliability, so once we heard what Matt and Kevin were being recognized for, it was shouting it from the rooftops from there on.”
Kevin and Matt are proud of what they’ve been able to achieve, but the benefits aren’t just limited to cost reductions or reliability improvements that help the plant’s bottom line. There are personal victories as well.
“With everything being so consistent and routine, it minimizes the chance for catastrophes to happen overall, including during the off-hours - so we don’t have to constantly worry about getting a phone call or a text to come in on a weekend or an off-day and solve an unexpected problem.”
Advice for Others
We asked both Kevin and Matt about the advice they would give to others who are looking to build and sustain a successful lubrication program. For plants who are getting started developing a world-class program, Matt recommends starting by looking at asset criticality. Assess your most critical assets and prioritize improvements from there. Try to demonstrate a quick win by fixing an issue with one or two machines and share the results with the team to get buy-in on larger improvement projects.
Kevin recommends modifying important gearboxes with breathers, sample ports, color-coded stickers, column sight glasses and the rest so that operators, inspectors and lubrication teams can catch warning signs earlier and avoid contamination or accidental lubricant mixing.
But most of all, Kevin said that to him, lubrication is all about consistency.
“Do it the same way every time - like taking samples, for instance; you know you are getting good baseline results when you are consistent in your procedures. If one month you keep the sample bottle protected from dust in the air with a plastic bag while you sample, but next month you leave the cap off of the sample bottle and don’t protect it at all, your oil analysis results will be skewed and useless for making informed decisions."
The Blue Buffalo Richmond plant continues to achieve reliability improvements through their dedication to lubrication best practices and hopes to encourage other plants to do the same. Blue Buffalo’s Joplin plant is already in the process of undergoing similar improvements, but the Richmond plant isn’t done yet.
“We know this is just the start of the celebration - not the finish line,” Megan told us. “While we are a 450,000 square- foot operation today, in the near future we will be significantly larger - and it’s because of the foundation these guys have built that enables us to make those investments and continue our reliability journey.”
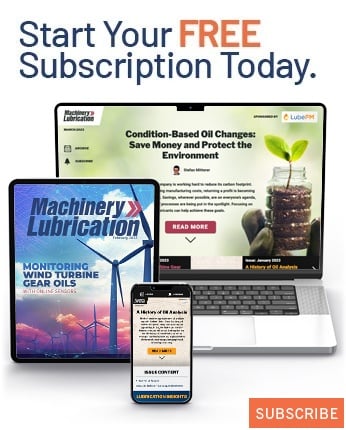